Why Laser Hot Wire Claddng Over Traditional Welding?

Laser hot wire cladding is a welding process that combines a preheated wire with a laser beam, and offers many benefits over traditional clad/hardface welding processes. It’s ideal for corrosion and wear resistance, when you have a very detailed part or when exact chemistry specifications need to be met. It’s also ideal if you have a situation where you require a metallurgical bond capable of handling strain that will not result in spallation of the coating.
Laser hot wire cladding provides high volume deposition rates with high travel speed and minimal heat input. However, unlike the DC or AC hot wire systems used in GTAW, which can easily reach a state where the heat wire will break into an arc, the Power Wave® power supply monitors the condition of the hot wire and suppresses any sustained arcing maximizing the temperature of the wire, which is quickly melted off in the puddle. Because this process is not “arc” dependent, it is not impacted by the same factors that impact an arc, such as speed and surface contamination. The result is that the process can be operated at higher speeds resulting in thinner layers, with less heat input, and therefore, less impact dimensionally or metallurgically to a part.
Because of these characteristics, laser hot wire cladding has a lower dilution rate compared to other arc welding processes. Where other arc processes of similar deposition rates (GMAW or GTAW) have the dilution rates as high as 30 percent, laser hot wire cladding is similar to laser powder which is often in the little as 5 to 10 percent.
Powder laser cladding also offers many advantages over traditional arc welding methods. With laser powder cladding, all of the energy to heat and melt the powder and the substrate is coming from the laser. By using laser hot wire cladding with the same laser powder, some of the energy is coming from the resistance heating of the wire, which means you can melt the same amount of material faster.
Working with powder has many drawbacks. For instance, because most cladding processes feed the powder into the laser beam, a certain amount – typically around 10% – does not go into the puddle and therefore is wasted. So if you are using 100,000 lbs. of powder a year at $20.00/lb. and losing approximately 10% of it, that’s $200,000 of lost revenue.
HOW LASER HOT WIRE CLADDING CAN SAVE TIME AND MONEY
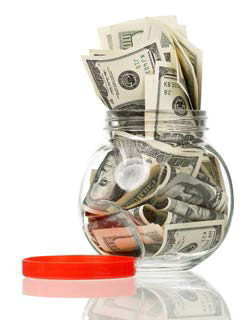
In many applications, cladding is done with either a stainless alloy or a nickel alloy using GTAW, but this process often requires multiple layers to achieve the correct chemistry and is a very low deposition process. Because laser hot wire cladding can deposit lower dilution material at two to three times the speed of GTAW, you may be able to clad larger areas using less material than what is possible by GTAW. Simple studies show that this could decrease the cladding cost per area by as much as fifty percent over GTAW.
Another potential application for laser hot wire cladding is for the repair/refurbishment of damaged or worn, high-value parts. Many industrial parts wear or are damaged in a very select area doing normal operation. Often these structures have tight dimensional tolerances and/or very specific metallurgical requirements. Many times as these areas are damaged, the parts are just replaced. With the low heat/low dilution/high deposition characteristics of laser hot wire cladding, it may be very economical to repair these high-value parts at a fraction of the cost of replacing. Also, by selecting the right material to clad, it may be possible to increase the life of the part over the un-clad part achieving improved performance. This can be a way of decreasing the costs of operations for a piece of machinery.